Measuring Deflection to Determine a Characteristic of a Cantilever
Measure layered material characteristics with precision using deflected collimated light
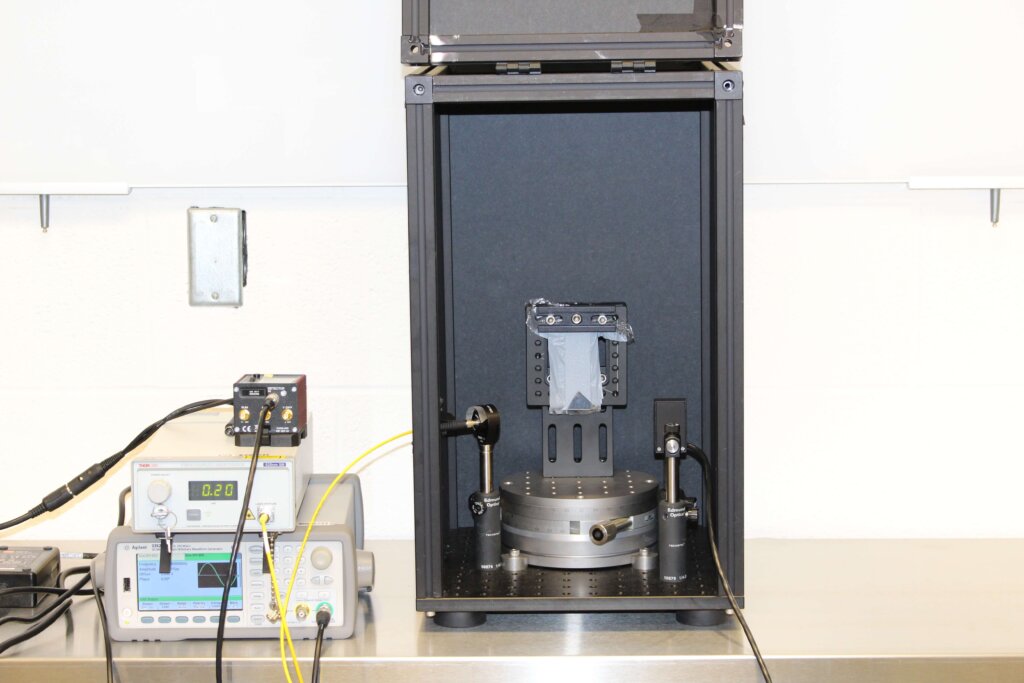
Many industrial applications require specific properties that a single material does not possess. To gain these properties, two or more materials may need to be layered. For example, coats of primer and paint can be applied to make steel corrosion-resistant, which is a desired characteristic for automobiles. The magnitude of adhesion between the two materials is critical to ensure the materials do not separate prematurely. Adhesion between two materials is related to the level of stress at the boundary between the two materials — the lower the stress, the increased ability to remain adhered.
Current standards for measuring levels of stress are subjective and at a higher resolution than what is possible with the human eye—in most instances, utilizing a low-precision, 12-inch ruler to measure changes. Even when changes are visually detectable, traditional methods introduce several sources of error, including changes in pressure during measurements, lower accuracy using millimeter gradients, and reproducibility between measurements.
By using a collimated beam of light, which is parallel and uniform, this technology accurately and precisely measures the characteristics of a processed, layered material without making physical contact.
This technique uses a cantilever method, where one end of a slightly arched strip of tested material is clamped to a fixed surface. A collimated beam of light shines on the tip at the opposite end of the clamped material. As the stress increases, the material will continue to curl (deflect) causing the reflected light to change the location where it hits the detector. This change can then be precisely and accurately measured, free from operator bias. By measuring the beam’s reflected position both before and after the material is processed (e.g., after a coat of paint is applied), the change in the beam’s reflected position can be used to calculate the material deflection caused by the newly applied layers. This measurement of induced deflection is then used to accurately determine the stress introduced into the bulk material by the process the material has undergone.
Characteristics of the material composition of a bi-metallic strip may also be determined from this system and method. In particular, mechanical stress (σ) can be estimated from the deflection measurement, Young’s modulus (E) from vibrations, and coefficient of thermal expansion (α) from temperature changes.
Benefits:
- Improved accuracy and precision: The system eliminates errors that are introduced by contact during measurements as well as human error using traditional methods. To achieve more accurate and precise results, the system can be placed in a box to shield it from extraneous light and/or isolate it against environmental vibrations.
- Advanced measurements: With multiple measurements from the position-sensitive light detector, the computer may create a plot of deflection vs. time.
- Expandable: The system can be extended with additional environmental sensors, such as a clock (e.g., to time the operation of a light source), thermometer, hygrometer, or environmental control systems such as a heater/air conditioner to set the temperature of the strip during measurement.
- Versatile: Measurements can be taken from the top or bottom of the strip and the material is not limited to two layers. The system also supports clamping the tested material from either the left or right edge or the top or bottom edge.
Applications:
- Quality assurance of coatings
- Temperature tolerance of coatings
- Stress limits of coatings
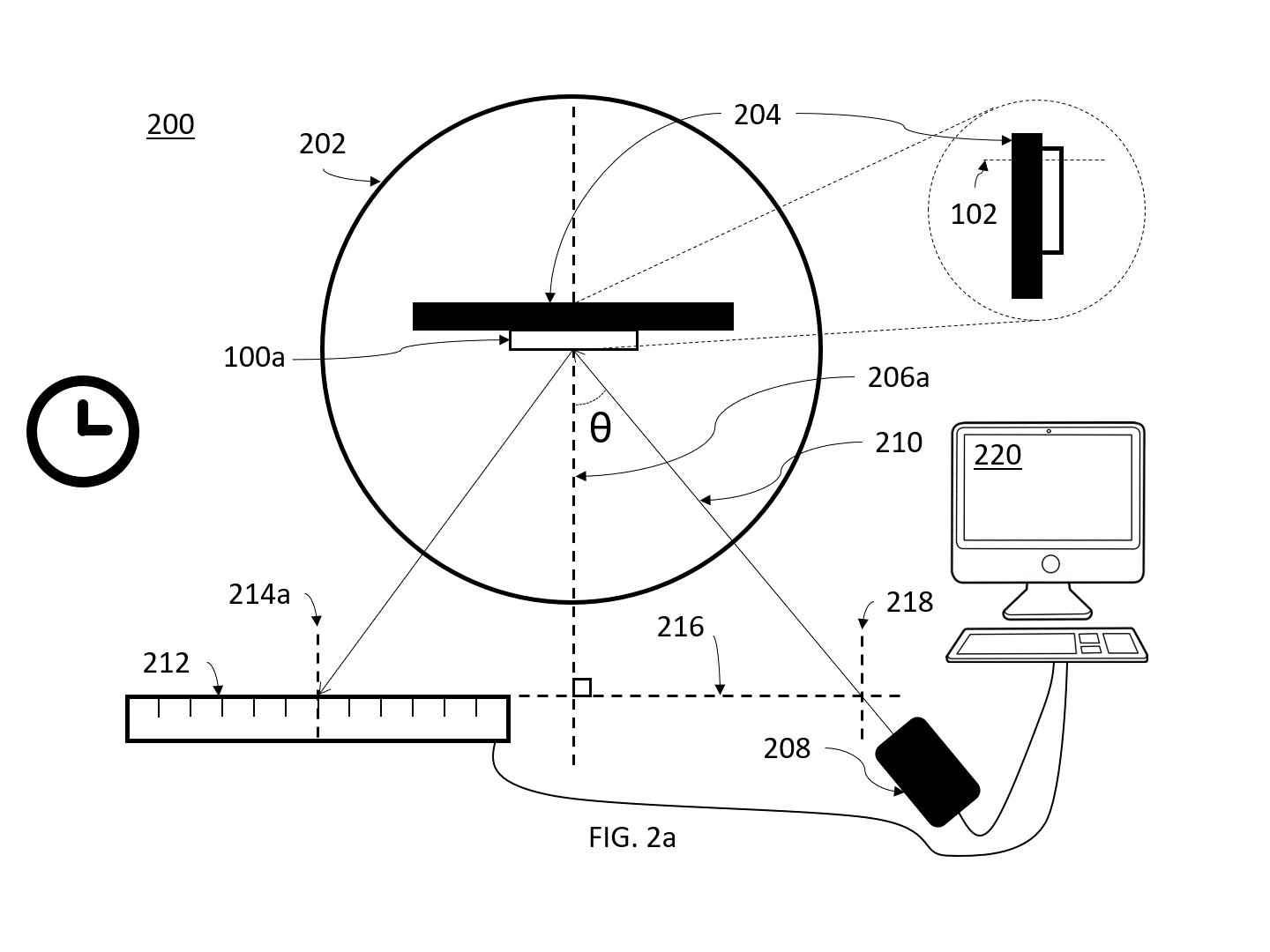